How Running Shoes Are Made: Behind the Scenes
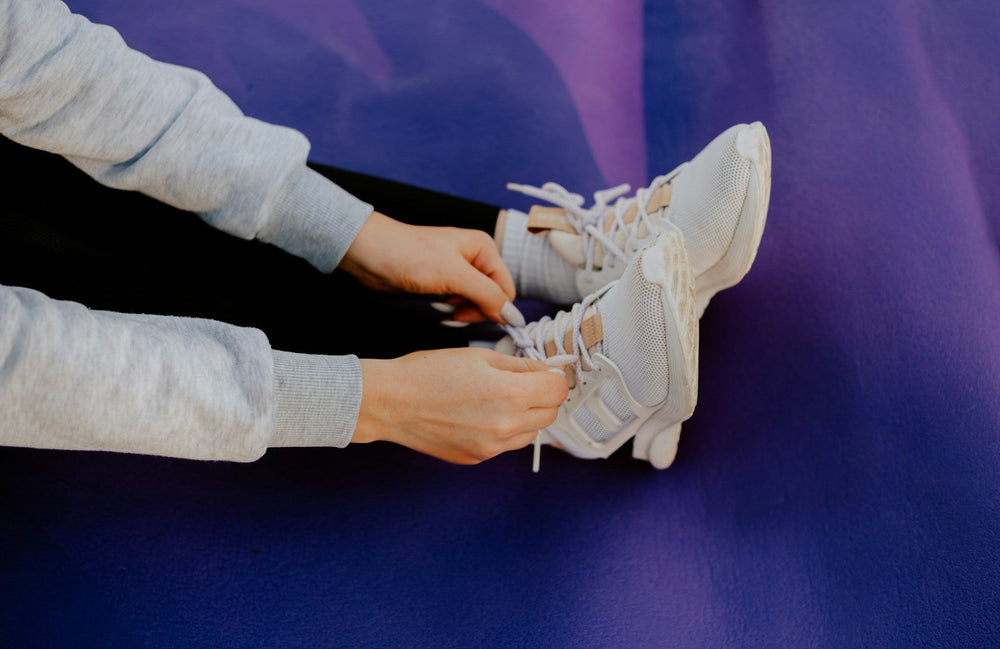
Ever wondered how your running shoes are made? These everyday items go through a detailed process before reaching your feet. From the choice of materials to final quality checks, each step ensures that the shoes provide comfort, support, and durability.
Materials play a huge role in the quality of running shoes. Modern running shoes are made using a mix of high-tech materials designed to offer the best performance. Choosing the right materials affects everything from the shoe’s weight to its flexibility and support.
Designing a running shoe starts long before it reaches the production line. Designers first come up with concepts based on the latest trends and research. These ideas are then turned into prototypes. Each prototype is tested to make sure it offers the best fit and performance.
Once the design is finalised, the manufacturing process begins. This includes stitching the upper parts, assembling the sole, and adding finishing touches. Each step is done with care to ensure the shoes are both strong and comfortable.
Quality control is the last and crucial step. It ensures that every pair of shoes meets high standards before they are sold. Rigorous testing is done to check for flaws and to guarantee durability. Only the best pairs make it to the shelves.
Get ready to dive into each of these steps and learn what goes into making your perfect pair of running shoes.
Materials Used in Running Shoes
Running shoes are crafted from a variety of materials. Each material serves a specific purpose, contributing to the shoe's overall performance. The main materials used in running shoes include synthetic mesh, foam, rubber, and sometimes leather.
Synthetic mesh is commonly used for the upper part of the shoe. This material is lightweight and breathable, keeping your feet cool and dry during long runs. The mesh also provides flexibility, allowing your foot to move naturally.
Foam is used in the midsole to provide cushioning. Modern foams like EVA (ethylene vinyl acetate) and PU (polyurethane) are popular choices. These materials absorb shock, reducing the impact on your joints and enhancing comfort.
Rubber is used for the outsole, the part of the shoe that makes contact with the ground. Rubber provides excellent grip and durability. Special rubber compounds can add extra traction and make the shoes last longer.
Occasionally, leather is used for certain parts of running shoes, like the upper or the heel area. Leather adds durability and can offer a snug fit. However, it is heavier and less breathable than synthetic materials, so its use is limited.
All these materials are carefully selected and combined to create a balanced shoe that offers comfort, durability, and performance.
The Design Process: From Concept to Prototype
The design process of running shoes starts with research and concept development. Designers study the latest trends, examine customer feedback, and look at advancements in technology. They use this information to create sketches and initial designs.
Once the concept is ready, digital tools like CAD (computer-aided design) software are used to create detailed models. These models help to visualise the final product and make necessary adjustments to the design.
Next, prototypes are developed. A prototype is a sample shoe made from the initial design. The prototype stage is crucial as it allows designers to test the shoe's fit, comfort, and performance. Various tests are conducted, including running trials and stress tests.
Feedback from these tests is used to refine the design. Changes might be made to the shape, materials, or any other aspect that requires improvement. Multiple prototypes might be developed before arriving at the final design.
After several rounds of testing and adjustments, the final prototype is approved. This prototype will serve as the blueprint for mass production. The approved design is then sent to the manufacturing team, who will start the process of creating the running shoes on a larger scale.
Manufacturing Steps: Stitching, Assembling, and Finishing
The manufacturing process of running shoes involves several key steps. Each step is designed to ensure the shoes are both strong and comfortable. The main steps include stitching, assembling, and finishing.
- Stitching: The process begins with stitching the upper parts of the shoe. Different pieces of fabric and materials are sewn together to form the shoe’s upper. Precision is crucial here to ensure a perfect fit and durability. The stitching must be strong but also flexible enough to allow for natural foot movement.
- Assembling: Once the upper parts are stitched, they are attached to the sole. This step involves glueing and pressing the upper parts onto the midsole and outsole. Special machines are used to make sure the bond is secure and will hold up during use. The alignment must be just right to ensure the shoe is balanced and comfortable.
- Finishing: The final step is finishing. This includes adding any final touches like logos, laces, and insoles. The shoes are then cleaned and inspected for any defects. Finishing ensures that each pair looks good and meets the quality standards set by the brand.
Throughout the manufacturing process, attention to detail is paramount. Each step is monitored to ensure that the shoes are made to the highest standards, providing both performance and comfort.
Quality Control and Testing
Quality control is an essential part of making running shoes. It ensures that each pair meets the high standards of performance, comfort, and durability. The process involves several stages of rigorous testing and inspection.
- Material Testing: Before manufacturing begins, the raw materials are tested for quality. This includes checking the strength, flexibility, and durability of the fabrics, foams, and rubber used. Only materials that pass these tests are used in production.
- Production Inspection: During the manufacturing process, each step is closely monitored. Workers inspect each piece to ensure that stitching, glueing, and assembling are done correctly. Any defects are corrected on the spot to prevent issues in the final product.
- Final Testing: Once the shoes are assembled, they undergo final testing. This includes stress tests to check for durability and comfort tests to ensure a good fit. Shoes are also tested for performance features like traction and cushioning. Only pairs that pass these stringent tests are approved for sale.
Final testing also often involves simulations of real-world conditions. This means running shoes are subjected to different surfaces and stress levels to mimic actual use. This thorough approach helps ensure that every pair is ready for the demands of running.
Conclusion
Running shoes undergo a complex and meticulous process from start to finish. Beginning with the selection of high-quality materials, moving through detailed design stages, and culminating in precise manufacturing steps, each part of the journey contributes to making a shoe that performs well and lasts long.
Quality control is the final barrier, ensuring that only the best shoes reach the shelves. This guarantees that each pair offers the right balance of support, comfort, and durability for every runner. The entire process highlights the dedication and craftsmanship involved in creating running shoes that meet the needs of runners everywhere.
At Sole Mate in Merthyr Tydfil, South Wales, we're committed to bringing you the excellence achieved through these processes. Whether you're purchasing in-store or browsing online, you can trust that our collection of running shoes represents the pinnacle of quality and innovation.
Are you ready for a superior running experience? Visit Sole Mate today to find the perfect pair of running shoes crafted with precision and care!